- What Are Parametric Constraints?
- Why Use Parametric Constraints in Mechanical Assignments?
- Applying Parametric Constraints in AutoCAD: A Step-by-Step Guide
- Practical Examples for Mechanical Assignments
- Best Practices for Applying Parametric Constraints
- Common Challenges and How to Overcome Them
- How Parametric Constraints Support Academic Excellence
- Conclusion
AutoCAD is one of the most versatile tools for engineers, architects, and designers. Among its many features, parametric constraints stand out as a powerful capability for enhancing the precision and efficiency of drawings. For students tackling complex mechanical engineering assignments, understanding and applying these constraints is crucial for achieving high-quality results. This guide dives into how parametric constraints can revolutionize your approach to solving problems in AutoCAD, specifically for mechanical applications. If you're looking for AutoCAD homework help, this comprehensive guide will also highlight practical tips and examples to simplify your learning process.
In mechanical engineering, precision and adaptability are key. Parametric constraints enable users to maintain strict control over dimensions and relationships between objects, ensuring that even the most intricate designs align perfectly. Whether you're a professional seeking to improve workflow or a student searching for mechanical engineering assignment help, mastering parametric constraints can save significant time and effort. This article will discuss their types, application process, and best practices for utilizing them in mechanical engineering projects.
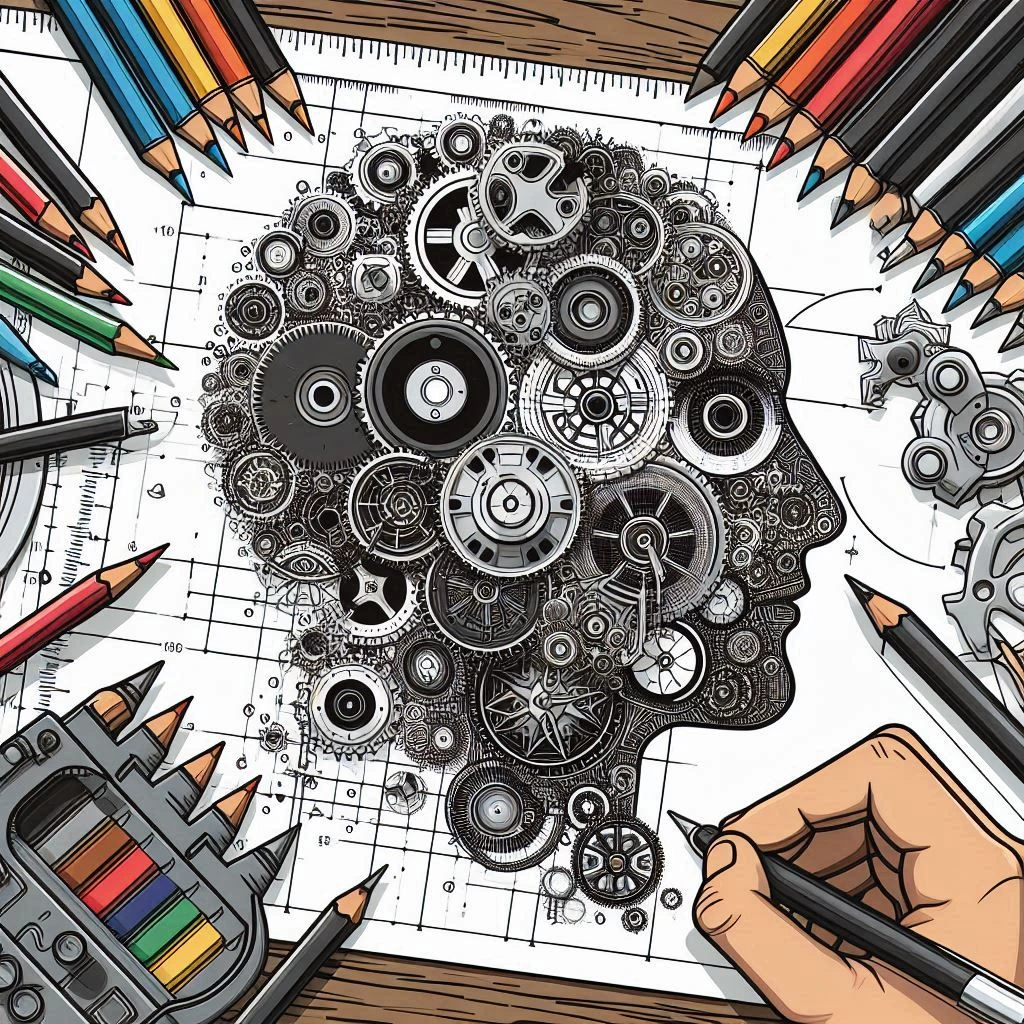
What Are Parametric Constraints?
Parametric constraints in AutoCAD allow designers to define and enforce specific rules or conditions within their drawings. These constraints can be geometric, controlling shapes and spatial relationships, or dimensional, regulating size and proportions. By applying these constraints, designers can automate adjustments and ensure that changes to one part of a drawing automatically propagate to other related parts.
Types of Parametric Constraints:
- Geometric Constraints
These ensure that geometric relationships are maintained between elements. Examples include:
- Parallel: Keeps two lines parallel.
- Perpendicular: Ensures lines are at right angles.
- Concentric: Maintains a shared center for circles or arcs.
- Coincident: Forces two points to occupy the same location.
- Symmetric: Mirrors geometry across a line of symmetry.
- Dimensional Constraints
Dimensional constraints specify exact sizes and distances. Examples include:
- Linear: Defines fixed lengths for lines.
- Angular: Sets precise angles between lines or edges.
- Radial: Controls the radius of arcs or circles.
- Aligned: Specifies distances along a specific axis.
Why Use Parametric Constraints in Mechanical Assignments?
The importance of parametric constraints in mechanical engineering cannot be overstated. Their application offers numerous advantages that make them indispensable for both professionals and students working on AutoCAD homework or real-world projects.
Key Benefits:- Enhanced Accuracy:
Precision is vital in mechanical engineering. Parametric constraints ensure that all components adhere to exact specifications.
- Efficiency:
By automating adjustments, these constraints reduce the need for repetitive manual edits, saving time and effort.
- Design Flexibility:
Constraints allow you to modify one aspect of a design without disrupting the entire drawing, making it easier to explore variations.
- Consistency Across Designs:
For assignments or projects with repetitive components, constraints ensure uniformity, reducing errors.
- Ease of Collaboration:
For students working on group assignments, constraints create a clear framework, making it easier to share and modify designs.
Applying Parametric Constraints in AutoCAD: A Step-by-Step Guide
Here’s how to effectively use parametric constraints in AutoCAD, especially for mechanical designs:
Step 1: Activate the Parametric Tab
- Open AutoCAD.
- Go to the Parametric Tab on the ribbon.This tab contains tools for both geometric and dimensional constraints.
Step 2: Define Geometric Constraints
- Select the object(s) you want to constrain.
- Choose the appropriate geometric constraint from the toolbar. For example:
- To make two lines perpendicular, select both lines and click the Perpendicular tool.
- To make two circles concentric, select the circles and apply the Concentric constraint.
- Ensure the constraints are visible by toggling the Show/Hide Constraints option.
Step 3: Apply Dimensional Constraints
- Use the Dimensional Constraint tool to assign specific values to dimensions like length, angle, or radius.
- Double-click a dimension to edit its value. Example: In a gear design, you can set the radius of a circle to a fixed value to ensure uniformity across multiple gears.
Step 4: Test and Adjust
- Modify one parameter and observe how other parts of the drawing adjust automatically. For instance, resizing a component in an assembly should maintain alignment and proportions if constraints are applied correctly.
Practical Examples for Mechanical Assignments
Example 1: Designing a Gear System
In a gear system, precise alignment and uniform tooth spacing are essential. By applying geometric constraints:
- Ensure that gear teeth are evenly spaced using the Equal constraint.
- Keep gear centers concentric for proper meshing.
Dimensional constraints can define tooth length and gear radius, ensuring that all dimensions are accurate and adjustable for different gear sizes.
Example 2: Assembly Drawing for a Machine
For assignments requiring an assembly drawing:
- Use Coincident constraints to align components such as bolts and holes.
- Apply Parallel constraints to ensure shafts and support beams are aligned.
Dimensional constraints can set the exact spacing between bolts or the length of a connecting rod, ensuring precision.
Best Practices for Applying Parametric Constraints
- Plan Before You Constrain:
Identify critical relationships and dimensions before applying constraints to avoid redundancy or conflicts.
- Use Constraints Sparingly:
Over-constraining a drawing can make it difficult to modify. Apply only the constraints necessary for your design.
- Organize Your Constraints:
Label constraints or use layers to separate constrained objects for better clarity, especially in complex mechanical designs.
- Leverage Dynamic Blocks:
Combine parametric constraints with dynamic blocks to create reusable components with adjustable parameters.
- Test Regularly:
Periodically test your constraints by making adjustments to ensure they behave as intended.
Common Challenges and How to Overcome Them
While parametric constraints are powerful, they come with challenges that can be frustrating for beginners.
- Over-Constraining:
This occurs when too many conflicting constraints are applied. Resolve this by removing redundant constraints or adjusting relationships.
- Slow Performance:
Complex drawings with numerous constraints can slow down AutoCAD. Use constraints judiciously and optimize your drawing by removing unnecessary elements.
- Error Messages:
If constraints fail, AutoCAD often provides hints about the issue. Carefully review relationships to identify and fix conflicts.
- Learning Curve:
For students seeking AutoCAD homework help, grasping constraints can be daunting initially. Practice with simple drawings before moving to complex designs.
How Parametric Constraints Support Academic Excellence
For students, mastering parametric constraints can significantly enhance the quality of their submissions. Professors value designs that showcase technical accuracy and professional-quality detailing. By using these constraints, students can:
- Produce polished assignments.
- Save time on repetitive edits.
- Explore creative solutions without compromising precision.
If you're struggling with your assignments, seeking professional mechanical engineering assignment help can provide tailored guidance and insights to improve your AutoCAD skills.
Conclusion
Parametric constraints in AutoCAD are indispensable for tackling mechanical engineering assignments with precision and efficiency. Whether you're designing complex assemblies or simple components, these tools empower you to create adaptable, accurate, and professional-quality drawings. By following the steps and best practices outlined in this guide, you can harness the full potential of parametric constraints and elevate your performance in both academic and professional settings.
If you're ever in need of expert assistance, don’t hesitate to seek AutoCAD homework help to refine your skills and excel in your assignments. With persistence and practice, you’ll master these powerful tools and stand out in the field of mechanical engineering.